A Lightbulb is Not a Brighter Candle: Why New Technologies Demand New Mental Models
New technologies don't just enable productivity gains within the confines of the status quo—they shape the very contours of what's possible. Henry Ford did just that with electricity in his factories.
If you're just joining us, this series follows the journey of a brilliant product manager, you. You've steered the product strategy of a company, Warehouse Software Inc, through 3 decades of technology disruptions. But in 2026, the company faces its biggest test yet - the ascendance of AI. The CEO has called an offsite, and the team is grappling with the implication of AI and how the flagship product, Warehouse Tracker, should respond to the change.
Here are links to the rest of the series:
Moments That Modernized: Four Decades of Tech's Tectonic Shifts
The Economics of Abundance: What Do You Charge When Software is Free to Produce?
Reinvent or Relinquish: You Can't Sell Horseshoes to People Who Don't Own Horses
The CEO steps forward, checking his watch. “We have a full agenda, so let’s dive in. First, our CMO will analyze how AI could reshape our customers’ world. Then in the next session, the CTO will explore enabling technologies we could tap. Finally, we’ll use the last session to define the next steps to build our future.”
He gestures to the CMO. “The floor is yours.”
The CMO stands, looking at the team. “To understand AI’s impact, we must see through our customers’ eyes."
"Why do warehouses exist?" he asks rhetorically before continuing
"Warehouses exist to store goods for future distribution. They provide an optimized location and facility for inventory to be received, sorted, tracked, and dispatched as needed to serve customer demands efficiently.
Though the industry has grown, its core mission remains unchanged.”
You nod, recalling Warehouse Software’s early days. The world looked different then, with most warehouses serving businesses. This meant delivery times could be slower, and warehouses could be located away from population centers and exorbitant rents. E-commerce quickened the pace. Delivery windows slammed shut, compressing from days into hours. Warehouses migrated into city hearts, paying steep rents to satisfy impatient urban shoppers.
“Warehouses are still labor-intensive, with 50-70% of costs from human work,” the CMO continues. “According to McKinsey, the industry spends $300 billion per year operating facilities. And inefficiencies abound, like dock scheduling, where 20-30% of trucks miss appointments, costing $50 billion annually. And if they don't miss their appointment, they're sitting at the yard idling their engines and chewing up precious driver time. "
The VP of Sales leans forward, always keen to cut through the fluff. “So tell me simply: how will AI change the warehouses?”
The group starts to chatter. Ideas emerged in fragments, bits of prophecy in search of a whole. AI bots could communicate with drivers, robotic dogs could do inventory checks.
Finally, the board member raises a hand. “It is too easy to slot each new tool into the familiar molds, finding new nails for hammers we already have. But that is to miss the point. We must form a new mental model to predict how AI might reshape the warehouse”
The CEO channeling the VP of Sales, asks, "What do you mean exactly?"
A lightbulb is not a brighter candle.
With a nod to Sundar Pichai, the CEO of Google, the board member invokes his analogy. "Sundar has often likened AI to electricity. Let's look back to how electricity changed manufacturing. In 1881, Edison established electricity-generating stations at Pearl Street in Manhattan and Holborn in London."
"Yet by 1900, less than 5% of mechanical drive power in American factories came from electric motors. The age of steam lingered. Why was that?"
The team pays close attention as the board member paces the room, as is his usual style
"We have to look at how factories worked in the world of steam power.” he explains.
Before the advent of electricity, factories operated around a central power source, such as a water wheel or steam engine
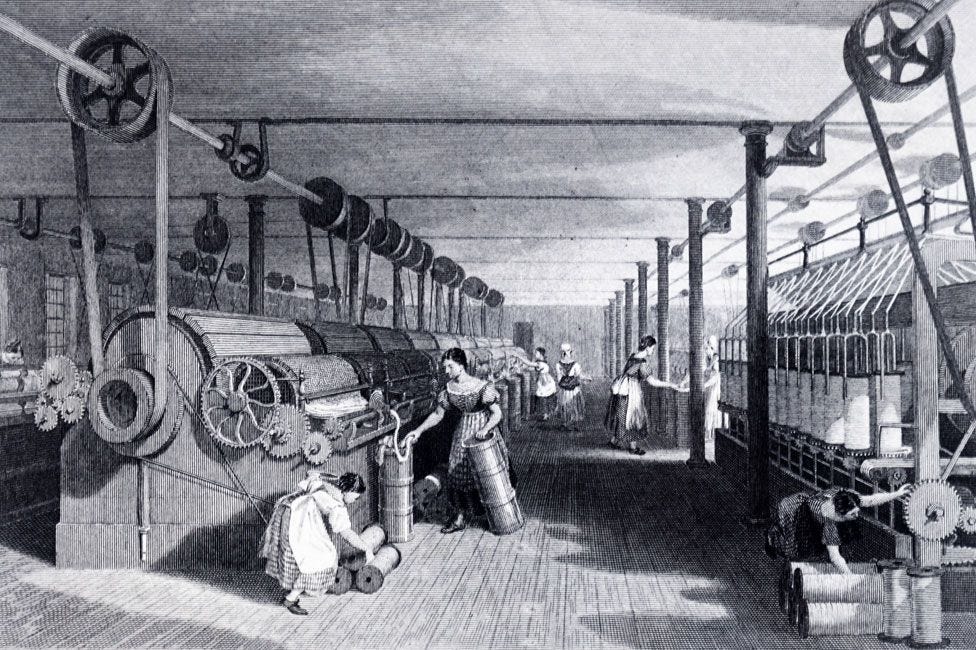
This power was transmitted to machines through a network of shafts and belts. Long metal shafts stretched across the length of the factory, and belts made of leather or rubber connected the shafts to the machines. As the central power source turned the shafts, the belts would rotate, providing the energy needed to power the machines.
This system placed limitations on factories. Machines had to be positioned along the shafts. Power would diminish as it traveled longer distances, so the factories were restricted in size. Making changes to the system was challenging because rearranging the interconnected machinery was a daunting task.
Electricity, of course, changed all of this. You didn't lose power over distance like with the shafts. You could run each machine at different speeds, and you could rearrange the machines since all it took was plugging them in.
Initially, the real advantages were modest. The transition to electric power improved machine safety and ease of use but cost more. The steam power infrastructure, with its investments in boilers, piping, and shafts, was already firmly in place. Electricity generation, in its infancy, was inefficient. Coal-powered plants could only convert 5-10% of coal's chemical energy into electricity, while steam power harnessed 50% or more of coal's energy. Some estimates even indicated that electric power cost 3-5 times more than steam power.
A new way to build factories
The true insight came when Henry Ford understood how electrification could transform automobile production in his factories. Ford had long sought to build a car that average Americans could afford, but he struggled to reduce costs enough to reach that goal. During a visit to Chicago's Union Stock Yards, Ford found the solution. There, he observed workers systematically disassembling animal carcasses into standardized parts.
Ford recognized that organizing assembly as a sequence of discrete steps, with each worker specializing in a specific task, could yield huge productivity gains. However, adopting such an assembly line approach would require an entirely new factory layout. The existing layout, based around a central steam power system, would not accommodate a smooth flow of materials and work-in-progress between specialized workstations.
Electrification provided the means to unlock Ford's vision. Once freed from the constraints of line shaft power, Ford could redesign the factory floor around assembly line principles. Cars flowed easily to specialized workstations, where focused workers efficiently completed tasks, accelerating the pace of production.
Though initially capital-intensive, the promise of higher volumes and lower unit costs justified the investment. Ford's gamble paid off.
Deploying electric-drive assembly lines at Ford's Highland Park plant boosted labor productivity by 500-700% between 1908 and 1915.
Ford was not alone in recognizing the potential of electrified assembly lines. Charles Nash implemented similar concepts at General Motors. However, other automakers failed to adapt quickly enough. Columbia Motors and Studebaker clung to small-scale craft production for too long, allowing Ford and GM to dominate the mass market.
The transition to electrified assembly lines and mass production enabled Ford and GM to outmaneuver rivals. While competitors were limited to artisanal manufacturing, Ford and GM unlocked economies of scale and speed, slashing costs and prices. By the time other automakers adopted these methods, Ford and GM had pulled far ahead, locking in significant competitive advantage.
The rise of AI may provide an opportunity to gain ground over competitors
"It's a once-in-a-lifetime opportunity to bring a gun to a knife fight," says the VP of sales, realizing the potential of what was yet to come.
"So some warehouse operators could leverage AI first and dominate the rest?" asks the CFO
The board member hesitates, noting, "Possibly, but innovators could also displace incumbents, as in the dot-com era. It was easier for startups to adapt before established players. Borders had existing stores Amazon didn’t need to maintain"
The VP of sales wasn't convinced. "But don't forget about Pets.com and Webvan. I see your point more generally, but the warehouse business isn't just something someone new can pick up easily"
"So what paths lie ahead for us? What is the mental model by which we should reevaluate the warehouse?" asks the CEO, eager to conclude.
You say, "Automation has always craved standardization. To code a computer system, we had to map every possibility into flowcharts. But now AI is starting to handle ambiguity, and we see that ability in robots. Just 10 years ago, robots needed pre-mapped environments to operate. Today, thanks to better sensors and SLAM (Simultaneous Localization and Mapping) algorithms, robots adapt to unknown spaces on the fly. This newfound freedom means we could have fully automated "lights out" warehouses for the first time. We're already getting a glimpse into that future in warehouses using Kiva robots.
Traditionally warehouses have aisles to allow humans to navigate to a shelf. But when a robot can move the shelf, you don't need aisles. You can store the product on movable shelves, increasing the warehouse density by 50% and click-to-ship speed by 5x. In Kiva warehouses, robots rule the center, and humans work at the perimeter. Our answer lies in asking what a warehouse looks like if we don't need humans to run them. "
The board member says, "Let's pretend there are no sunk costs, and we were starting today. Would we build this unique 10x advantage and sell it to existing operators or enter the market ourselves?"
"If AI disrupts software and makes it 'free' by automating software development, we may have no choice," the CEO says.
Silence descends.
“We must first understand how AI could transform software,” you suggest. “Let’s see what we learn in the next session.”
The team adjourns for lunch.